Automation
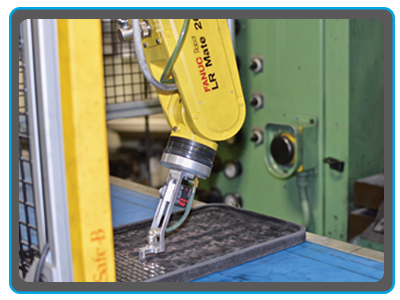


Western Sintering Automation of Metal Components at Their Finest!
When you want to compete in manufacturing, the first thing you must do is figure out how to automate your processes. Repeatable processing of any kind needs the help of robotics that are programmed to do the mundane tasks humans tire of. Initially the human sets up the job, programs the robot, proves the process and perfects it. Then, it’s time to turn it over to the one that never tires, never needs breaks, never goes to the bathroom, doesn’t call in sick, doesn’t go on vacations, and will run through the night until you show back up in the morning, rested and ready to start another project. That’s right, it’s our buddy the never tiring robot.
Western Sintering Company (WSC) excels at problem solving, engineering, and offering their customers solutions that helps them fill their customers’ supply chain with repeatable quality product every time. Instead of hogging out a part from a hunk of raw metal, WSC furnishes a pure powder metal solution, and engineers a tool molding process that forms a metal powder solution. The metal powder is pressed with many tons of force to a calculated density, pressed with tons of force to a near net shape, prior to heating it up to the highest in sintering temperatures to allow the powder metal to bond together and meld to a finished part. Yes, their expert engineers create a process that allows a near perfect part for their machine shop to CNC program what we call a ‘Kiss’ in the industry, that takes the pressed sintered part to final processing that is pressed Quickly, uniformly, consistently, and faster than most forms of manufacturing, including 3D manufacturing.
It’s hard to find qualified humans in manufacturing. Bringing on robotics has transformed Western Sintering.. Fast is good! But, haste does not make waste in WSC’s engineering process.
Once the process is perfected with tooling, the right density, the perfect heat processing, then the process has to be formulated into the robot’s realm, one that continues to be monitored by WSC’s team. The more steps that can be automated, the more possible problems or inconsistencies are ruled out, and complete perfection is inherent.
WSC started out the old fashion way many years ago. Founder, John Rector started out at the age of 26 leading a dozen tool and die makers at the DuPont plant in Kansas City forming 16mm cannon cartridges for the war. John received his first major promotion because he could compute square roots in his head. DuPont sent him to the ‘Manhattan Project’, a secret weapons project in the eastern Washington desert to perfect his work and processes. John designed a process to sinter aluminum boron that was control rod material for the historic B reactor. John envisioned that rather than machining parts the common way from raw solid material, he could press powder with tons of pressure into a form and take it to the ovens to heat it to a molded, net, almost perfect shape and density. Once molded these metals or pucks could be minutely machined into a perfect part quickly and uniformly.
Companies have utilized WSC for this unique process for years and as production moved to thousands; it was imperative to automate the process. Jeff Wood, President of WSC and Dave Morasch, Vice President of WSC worked together to create an automated process that could be tracked, improved, and moved to a production scale of manufacturing. Since robotics and pressing metal aren’t widely implemented this management team sent two of their expert team to the Fanuc factory. Once trained, WSC was able to take the automated pressed puck from the 200 ton press machine to sintering trays and be placed in position for the heating process. When you are dealing with thousands of parts this is a Godsend for the operating staff as the mundane process can be taxing and not to mention a boring feat for humans.
As an ISO9001 company, WSC maintains an expertise in many varieties of metals from alloy steel, stainless steel, copper, brass, nickel silver (white brass), bronze, aluminum, and many others. WSC aligns approved outside processing partners to plate the parts to a component that once quality checked by their team, is packaged carefully and shipped to the customers for a finished part that is ready to arrive on time at their customers’ production line. It sounds easy. But when you are working with powdered metal, precision molds, 200 plus tons of pressure, handling, heat treating or sintering it is a delicate game of making sure your process forms the solid mass that is placed in a perfect atmosphere that yields the perfect end result, once a solid piece of particles that are deposited in the right density for melding in the sintering process. Wow! WSC has maintained their quality service by continuing to add state of the art processing, from 200-ton compacting press machines, 17 zone sintering controlled furnaces, to now robotics that aid in handling the pressed parts off the presses. This all adds to the goal of WSC to move the production of their customers parts into a perfect state of production that will allow no human error, and aid in the production of finished parts that meet their customers production schedules of higher volume parts, on time. If you are looking for an excellent choice for production where precision is required, look nowhere else but, Western Sintering Company.
For more information on Western Sintering Inc., WSC and how they can automate your processes contact Dave Morasch at 509-375-3096.
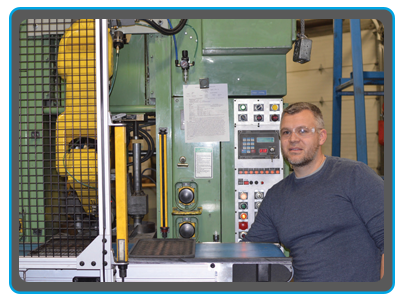

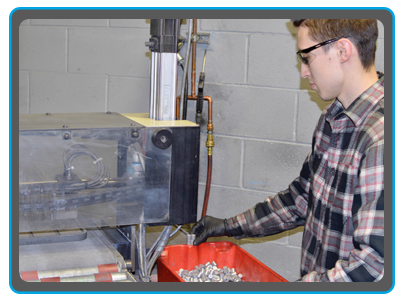
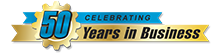
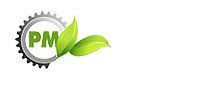